Soldadura, comprobación, manipulación a la perfección por Gebr. Binder GmbH
La célula robotizada Yaskawa convence en la producción de grandes volúmenes
En la empresa suaba Gebr. Binder GmbH Metallwarenfabrik todo tenía que ir rápido. Un pedido a gran escala para la fabricación de alrededor de medio millón de piezas de chapa al año exigía una solución de producción de primera clase. Junto con Yaskawa Europe, la empresa se propuso crear una célula de producción que estableciera estándares en términos de producción, precisión y disponibilidad.
- Industrias
- Metal
- Aplicaciones
- Manipulación
- Soldadura por puntos
- Control de calidad
- Cliente
- Gebr. Binder GmbH
El proveedor suabo de la industria del automóvil Binder goza de una excelente reputación en el sector. Esta empresa familiar con sede en Neenstetten se considera fiable, orientada al cliente e innovadora, y suministra a fabricantes de equipos originales de todo el mundo. Con sus aproximadamente 800 empleados, se dedica a la tecnología de conformado y procesamiento de chapa metálica. El hecho de que un importante fabricante alemán de automóviles se dirigiera a esta empresa en rápida expansión con un pedido para la producción en serie de una construcción de chapa metálica destinada a alojar las baterías de a bordo de determinadas series de vehículos, habla en favor de la reputación y los resultados de la empresa.
Thomas Pflüger, ingeniero mecánico y responsable del departamento de tecnología de unión y soldadura de Binder Production: «Manejar un pedido de esta magnitud -la capacidad máxima de producción es de alrededor de medio millón de bastidores de baterías al año- no sería posible, evidentemente, sin la inversión en un sistema completamente nuevo y altamente automatizado que integra los procesos necesarios de soldadura por puntos, comprobación, firma y manipulación.»
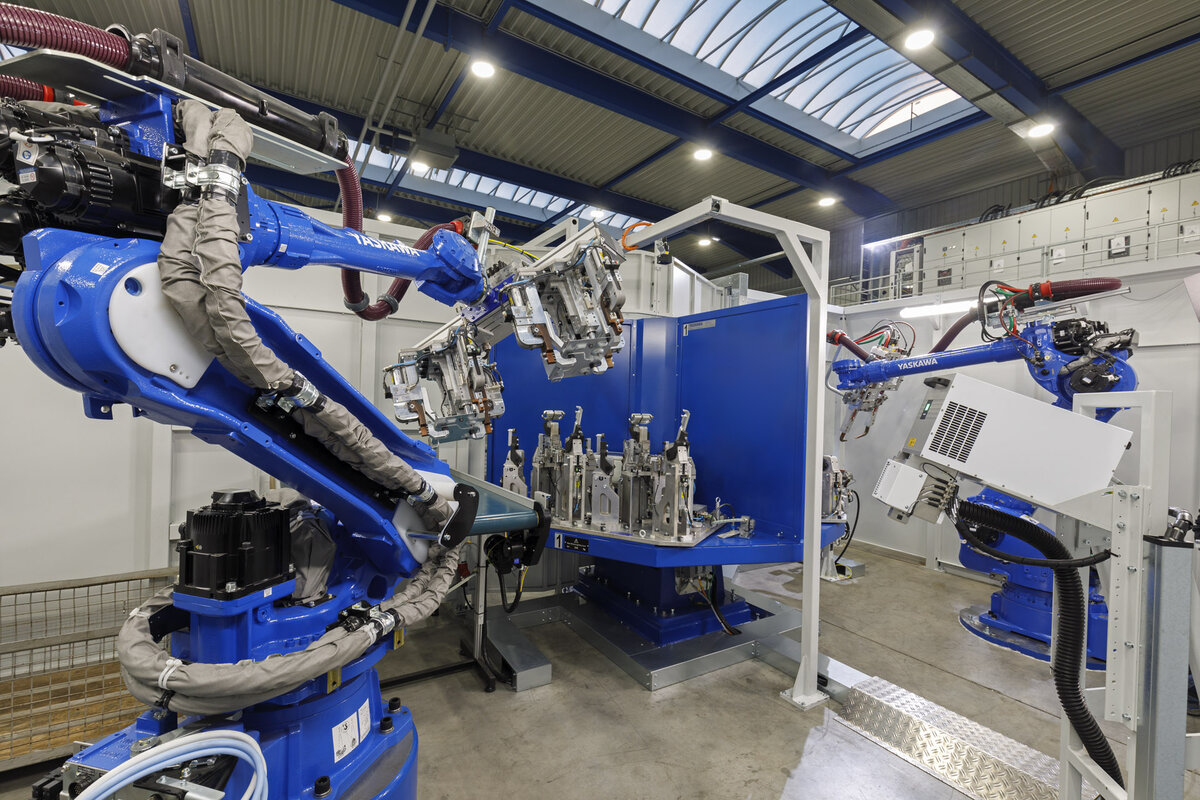
Imagen: Vista del interior de la célula: a la derecha el robot de soldadura por puntos, en primer plano la estación de firma láser y a la izquierda el robot GP88 de seis ejes para manipulación.
Un operario, dos robots, tres estaciones
Los ingenieros de Binder empezaron a trabajar inmediatamente en un primer borrador, que esbozaba conceptualmente las estaciones esenciales de la nueva célula robotizada. Este concepto constituyó la base para Yaskawa Europe, a cuyos especialistas se confió la planificación detallada y la implementación del sistema completo.
Roland Hermann, Senior Key Account Manager de Yaskawa, recuerda: «Todos sabíamos que sólo podríamos alcanzar las especificaciones de tiempo de ciclo para esta pieza de producción en serie con el uso de dos robots de seis ejes, uno para la soldadura por puntos y otro para la manipulación general. Además, una solución de tres estaciones prometía ser la más viable, ya que permitía implementar todos los procesos en paralelo y, por tanto, independientemente del tiempo de ciclo. Mientras que la inserción en la primera estación es manual, en la segunda se puede soldar y en la tercera se puede comprobar y retirar».
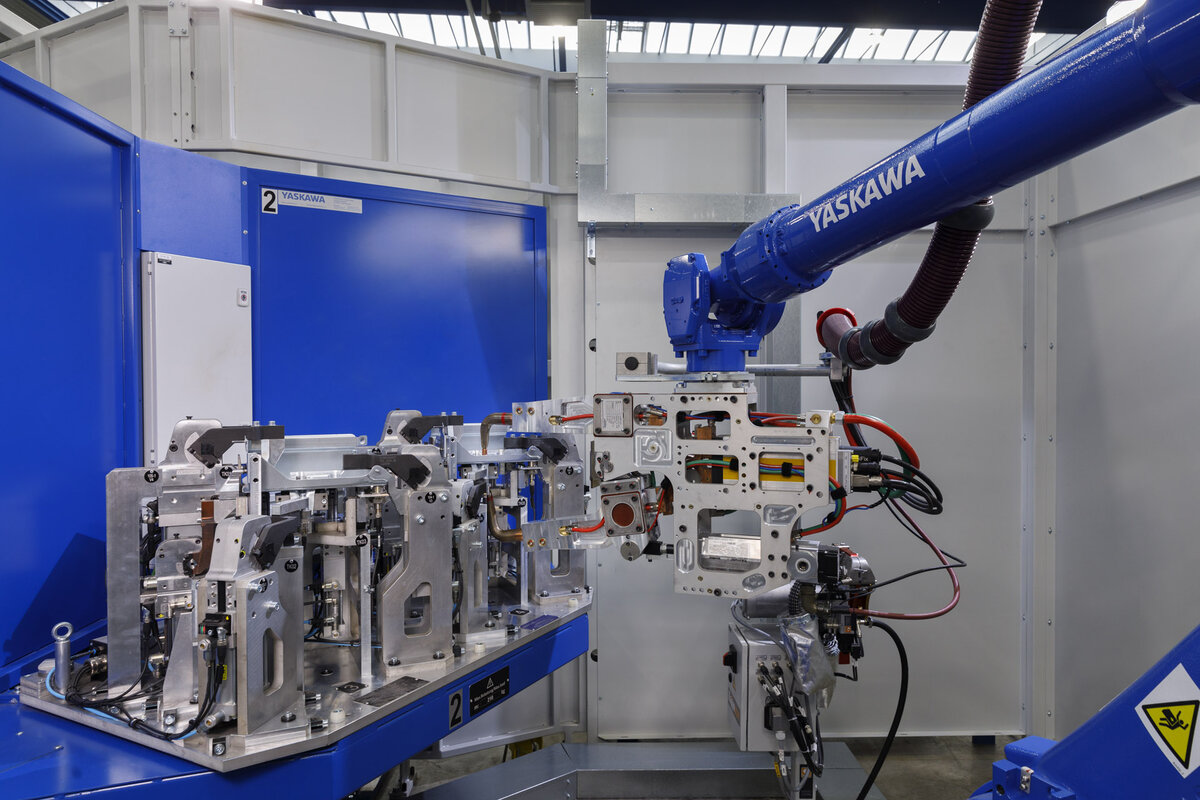
Imagen: La Yaskawa GP88 está equipada con una compleja pinza doble para tareas de manipulación.
Solución bien concebida con detalles convincentes
El sistema recientemente puesto en servicio convence por sus numerosos detalles bien concebidos y sus requisitos de espacio muy reducidos. Huelga decir que cada componente se seleccionó pensando en el máximo rendimiento y fiabilidad.
Empezando por los robots: un esbelto Motoman de seis ejes y alto rendimiento de la serie SP asume la tarea de la soldadura por puntos, mientras que un rápido e igualmente preciso GP88 se encarga de los procesos de manipulación. Thomas Pflüger: «No hubo que discutir mucho a la hora de seleccionar los robots. Ya estamos utilizando varios robots Yaskawa y sabemos que los «robots Motoman» cumplirán nuestros requisitos al cien por cien. Son corredores de resistencia muy fiables que superan con nota cualquier maratón de producción».
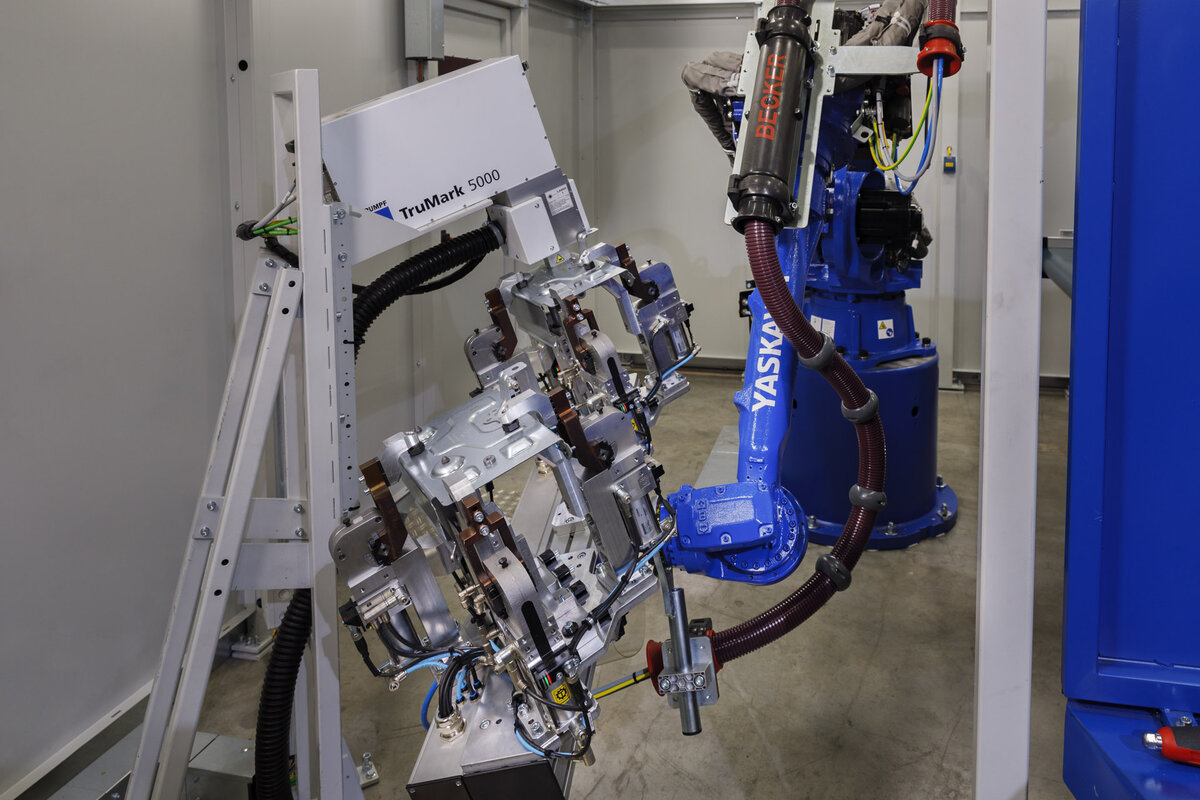
Imagen: Asunto complejo - la GP88 con dos componentes en la pinza para la firma láser.
Diseñados para la máxima disponibilidad
Gracias a su calidad, todos los demás componentes deben garantizar también una alta disponibilidad. Se utilizan, entre otros, una pistola de servosoldadura de construcción ligera, una estación automática de limpieza y cambio de las caperuzas de los electrodos, un sistema de cámaras 2D de Cognex para el aseguramiento de la calidad, un láser de marcado de clase 1 de Trumpf, un PLC de Siemens y, por supuesto, un sistema de control de soldadura de última generación de Bosch Rexroth con supervisión permanente de los parámetros de soldadura.
Lo más destacado del sistema es el posicionador vertical de 3 estaciones, que está equipado con dos nidos de fijación por estación, para procesar en paralelo seis bastidores de batería. Roland Hermann: «Lo que lo hace especial es que esta solución se basa en un producto estándar de Yaskawa, el posicionador R-1000, que tiene un eje de rotación vertical. Suministramos este accionamiento básico modular con una placa base diseñada para dispositivos automáticos y ejecutamos la solución de tres estaciones. La rotación de 120 grados necesaria para la aplicación se implementa en el funcionamiento exclusivamente mediante software. El eje de posicionamiento está integrado en el sistema de control maestro del robot como un eje robótico de pleno derecho».
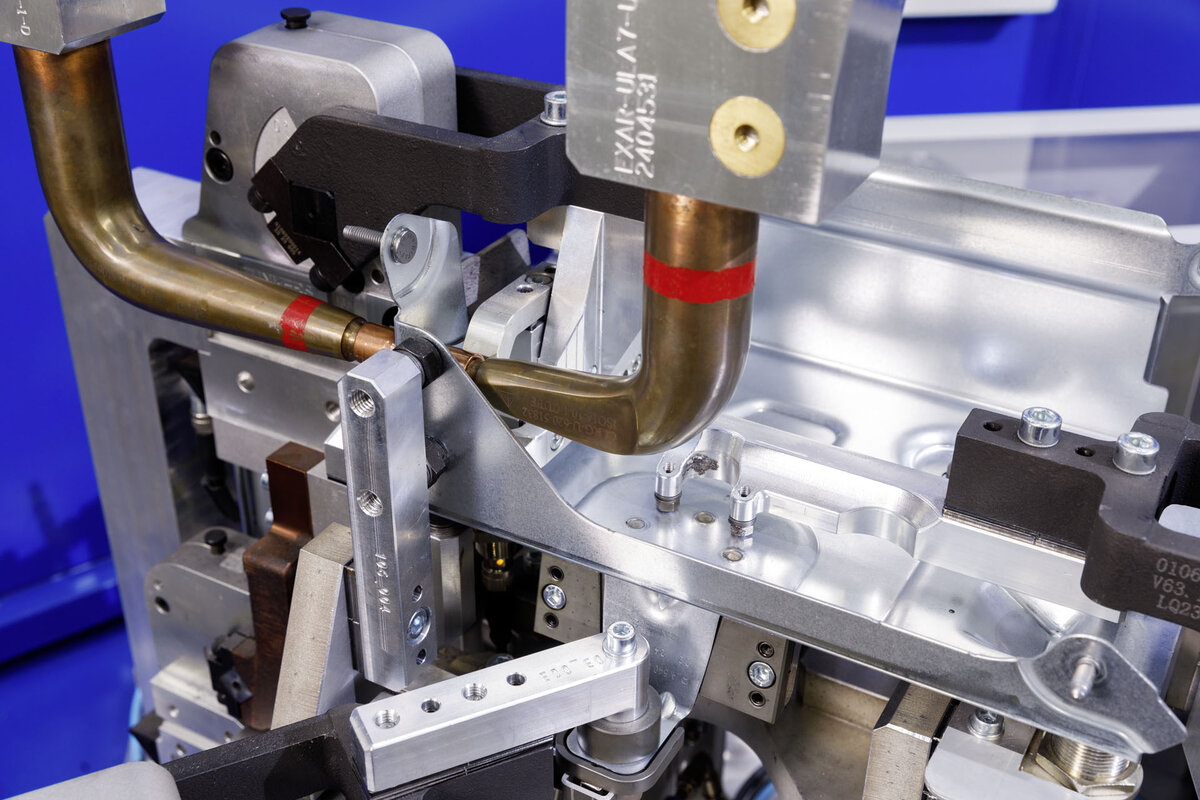
Imagen: Los puntos de soldadura son a veces de difícil acceso, pero los programadores han hecho un trabajo excelente.
Determina la duración del ciclo: limpieza y sustitución de los capuchones de los electrodos
El estado de los capuchones de los electrodos es, por supuesto, decisivo para el proceso. La limpieza periódica de los capuchones mediante el fresado de la capa de zinc resultante y la sustitución tras un número determinado de operaciones de fresado se realizan de forma totalmente automática en la estación, sin intervención del operario. Dado que este proceso es uno de los que determinan el tiempo de ciclo, el posicionamiento de la estación de limpieza y cambio se seleccionó para garantizar las distancias de desplazamiento más cortas del robot.
Una vez finalizada la soldadura por puntos, el posicionador vuelve a recorrer un ciclo de 120 grados hasta la estación tres. Aquí -todavía en la fijación- se comprueba con una cámara la presencia y el ajuste correcto de los pasadores roscados y una tuerca. Una vez superada con éxito la prueba de calidad, la esbelta Motoman GP88, con su doble pinza neumática, retira simultáneamente ambos componentes y pasa a la estación de marcado por láser, donde los componentes reciben un código de letras y números que sirve para la identificación y trazabilidad de la pieza.
En la aplicación de la señalización se puede prescindir de dispositivos adicionales especiales de protección láser, ya que los componentes son guiados por el robot de manipulación hasta el cabezal de marcado de forma segura para el láser. Esto se consigue aplicando una presión predefinida desde el robot a los elementos de sellado del cabezal de marcado, cumpliendo así los requisitos de seguridad láser. En el último paso, el robot de seis ejes deposita las piezas OK en una cinta transportadora que se descarga manualmente. Los componentes que la cámara o el sistema de control de soldadura determinan que no están bien son depositados por el robot manipulador en una caja separada en la que se controla la cantidad.
El control general del sistema se realiza mediante un PLC Siemens S7 de nivel superior con visualización, al que están conectados los dos controladores de robot Yaskawa YRC 1000 a través de Profinet. Desde su puesta en marcha, el sistema ha funcionado sin problemas tanto en lo que respecta al software como al hardware. En Binder nunca se han arrepentido de haber optado por Yaskawa.
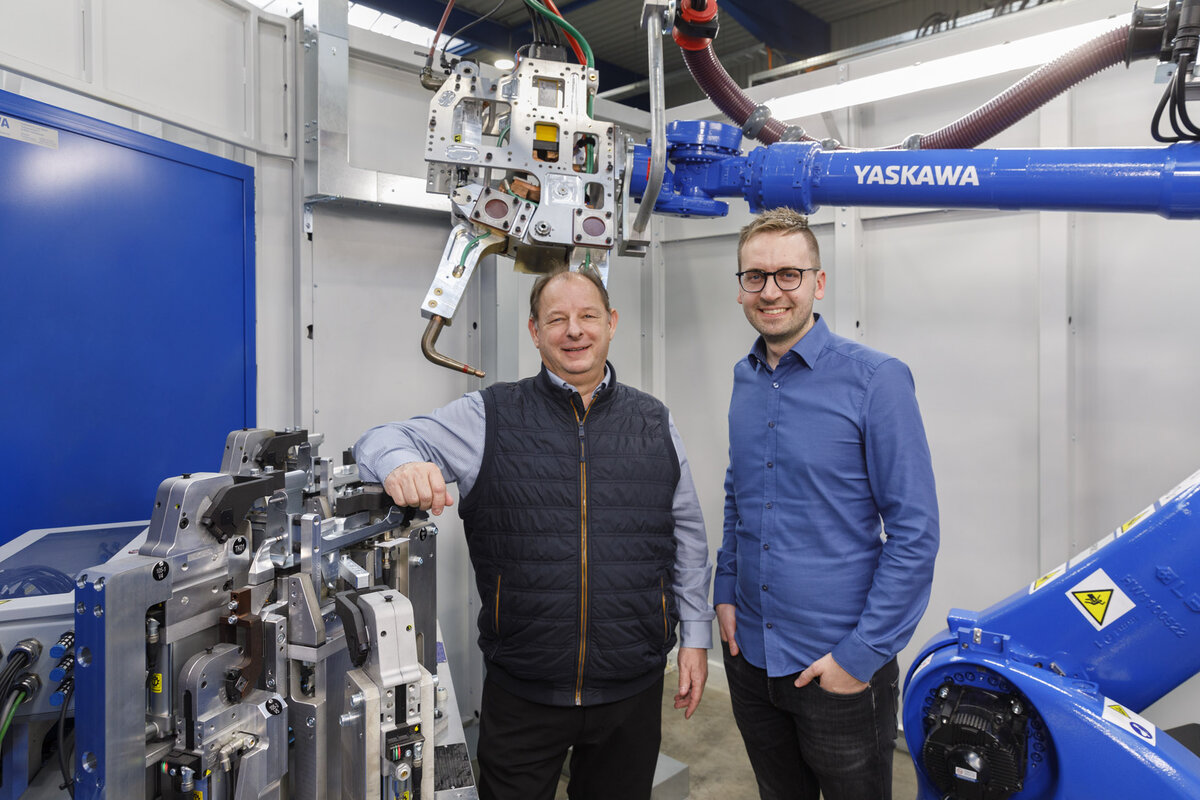
Imagen: Roland Hermann (izquierda), de Yaskawa, y Thomas Pflüger, de Gebr. Binder, se felicitan por el éxito del proyecto.
Texto: Ralf Högel
Fotos: YASKAWA Europe GmbH